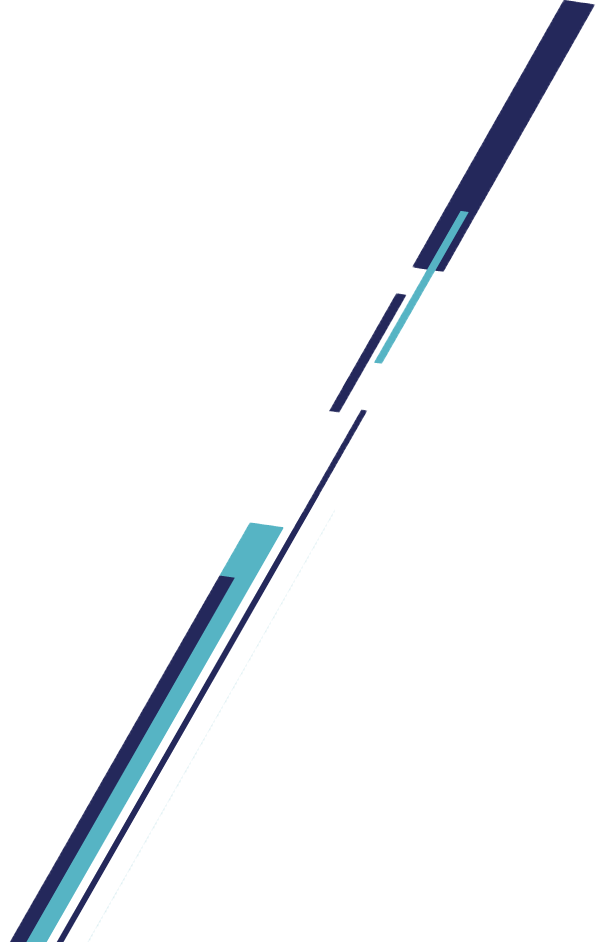
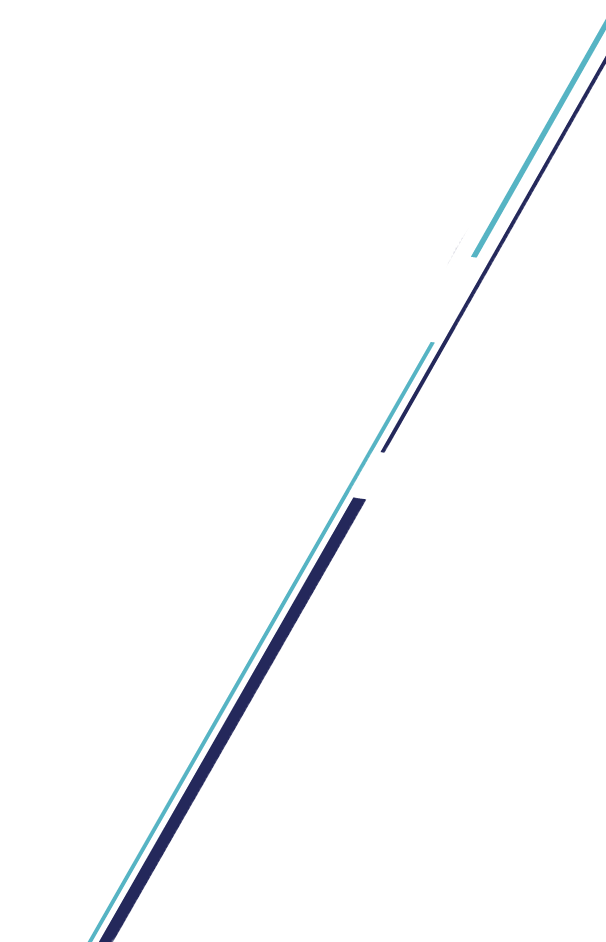
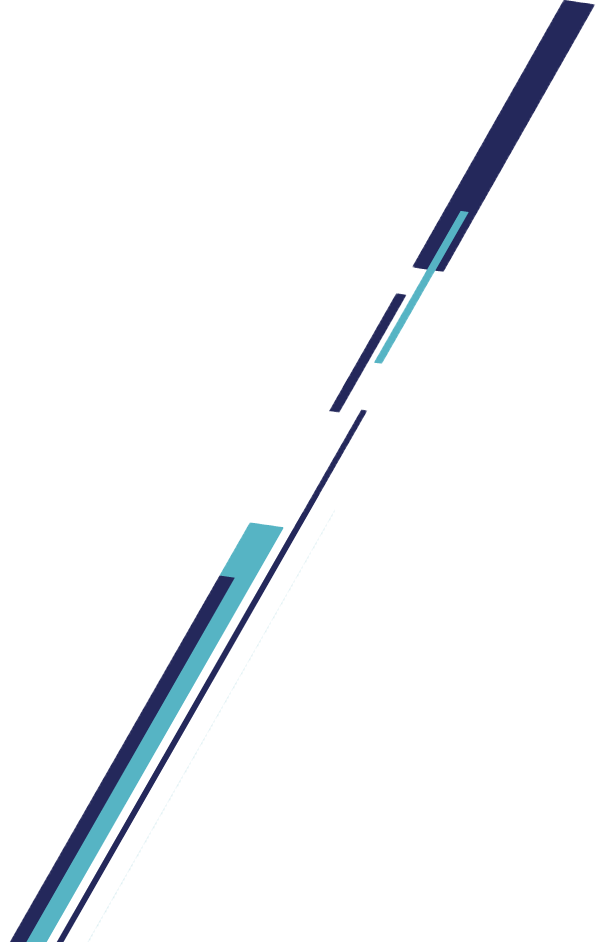
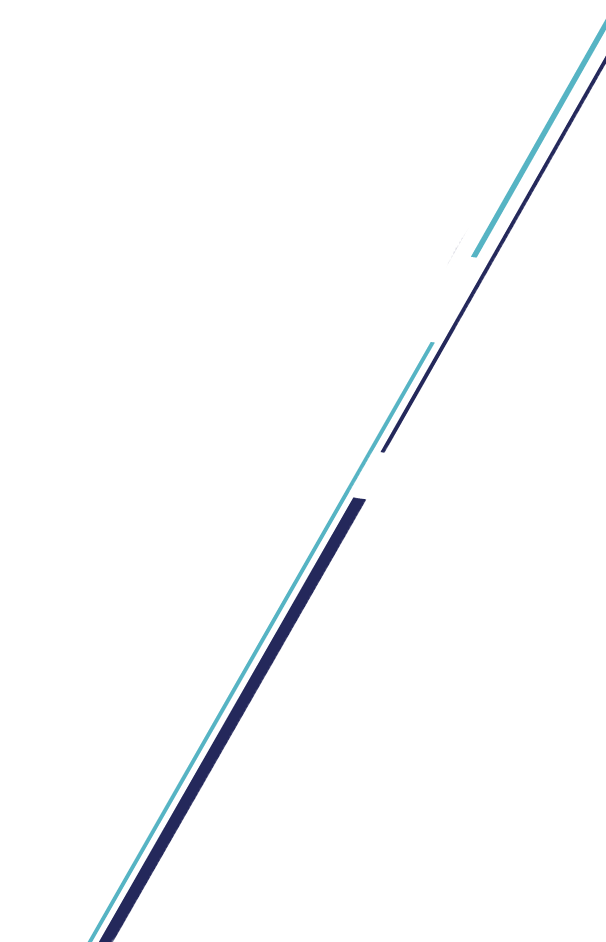
Thermoforming is the process of shaping objects.
Thermoforming is the process of shaping objects from polymeric materials such as:
- styrene plastics, e.g. PS (Polystyrene) or ABS (Acrylonitrile-butadiene-styrene),
- pololefins such as: PE (polyethylene) or PP (polypropylene),
- PVC (polyvinyl chloride),
- PET (polyethylene terephthalate),
- PMMA (Polymethyl methacrylate),
- or biodegradable plastics – PLA (Poliactide).
The process consists in heating the material in the form of plates or foil to the state in which it reaches plasticity and then forming it to the desired shape by means of pressure or underpressure.
Thermoforming can be divided into 4 types due to the thickness of the material used:
- Thin foils up to a thickness of 0.25mm,
- Small film thickness from 0.25mm to 1.5mm,
- Thin plates from 1.5mm to 3mm,
- Boards from 3mm to 13mm thick.
The thermoforming process can be described in four basic steps:
- Assembly of material on the form,
- Heating the raw material to obtain plasticity,
- Vacuum or pressure forming,
- Cooling.
Depending on the type of product to be made by thermoforming, 2 techniques can be used:
- Negative forming
In this case, the material is on the upper part of the concave mold. After heating to the desired temperature, the process of pressing elastic material into the concave mold cavity occurs.
- Positive forming
The difference between the types of thermoforming is mainly due to the shape of the mold used in the process. During positive molding, the form should be convex and the material after heating is drawn on the mold.